SurfPRO tools
Surface finishing systems for plastic and metal
SurfPRO tools are advanced surface finishing/roughness reduction systems developed for metal, polymer and composite 3D printed parts, and with fields of application that range from automotive to aerospace, from medical to consumer goods.
Based on the Microfluid process, the systems make use of media as conveying vector for the 3D printed objects, while the surface finishing is performed by in-house developed abrasive gels, capable to reach the most hidden features of the processed parts.
Depending on customers’ needs, the SurfPros can work as standalone systems as well as in conjunction with our VirboBlasts (to even the surface rugosity before the finishing process) and with electrochemical systems.
Not your average Vibratory finishing system
Traditional tribofinishing, also called tumbling or vibratory finishing is a widely known process for mass-finish metal or plastic parts.
Whether you effectively need to process a large number of 3D printed parts (which is a typical SLS and Binder Jetting scenarios) or a small batch (FDM or SLM scenarios), the process is the same: parts have to be processed through different abrasion stages, from the most aggressive to the gentler.
Usually, the process requires up to 4 vibratory systems, each loaded with different tumbling media, and the parts have to be manually moved from one machine to another every time a cycle ends.
Or, you could have just one machine, and replace media between each step (after a careful cleaning), but that’s an even less optimized workflow, economically inefficient.
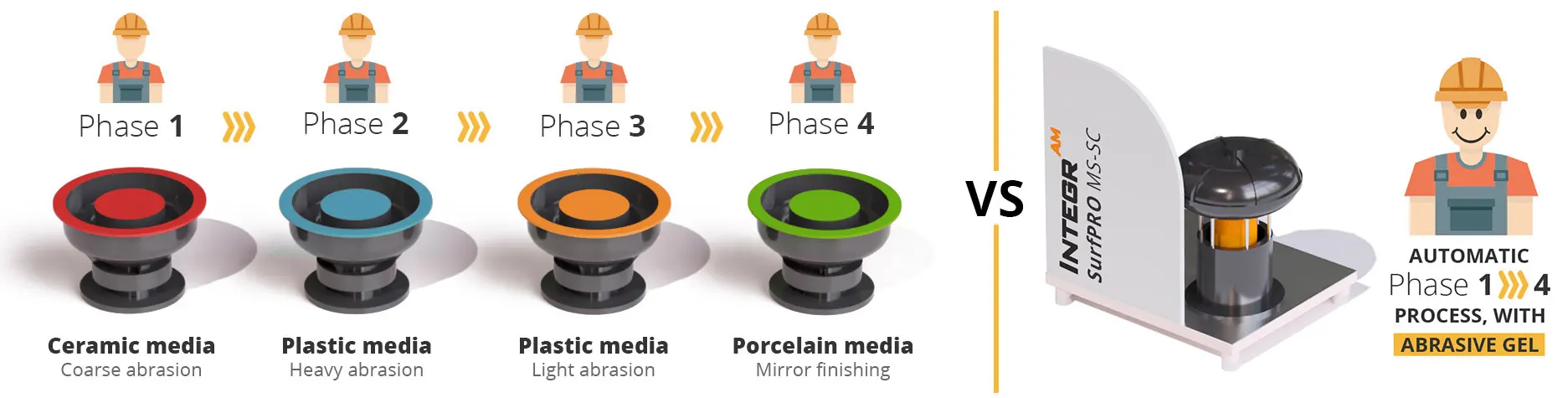
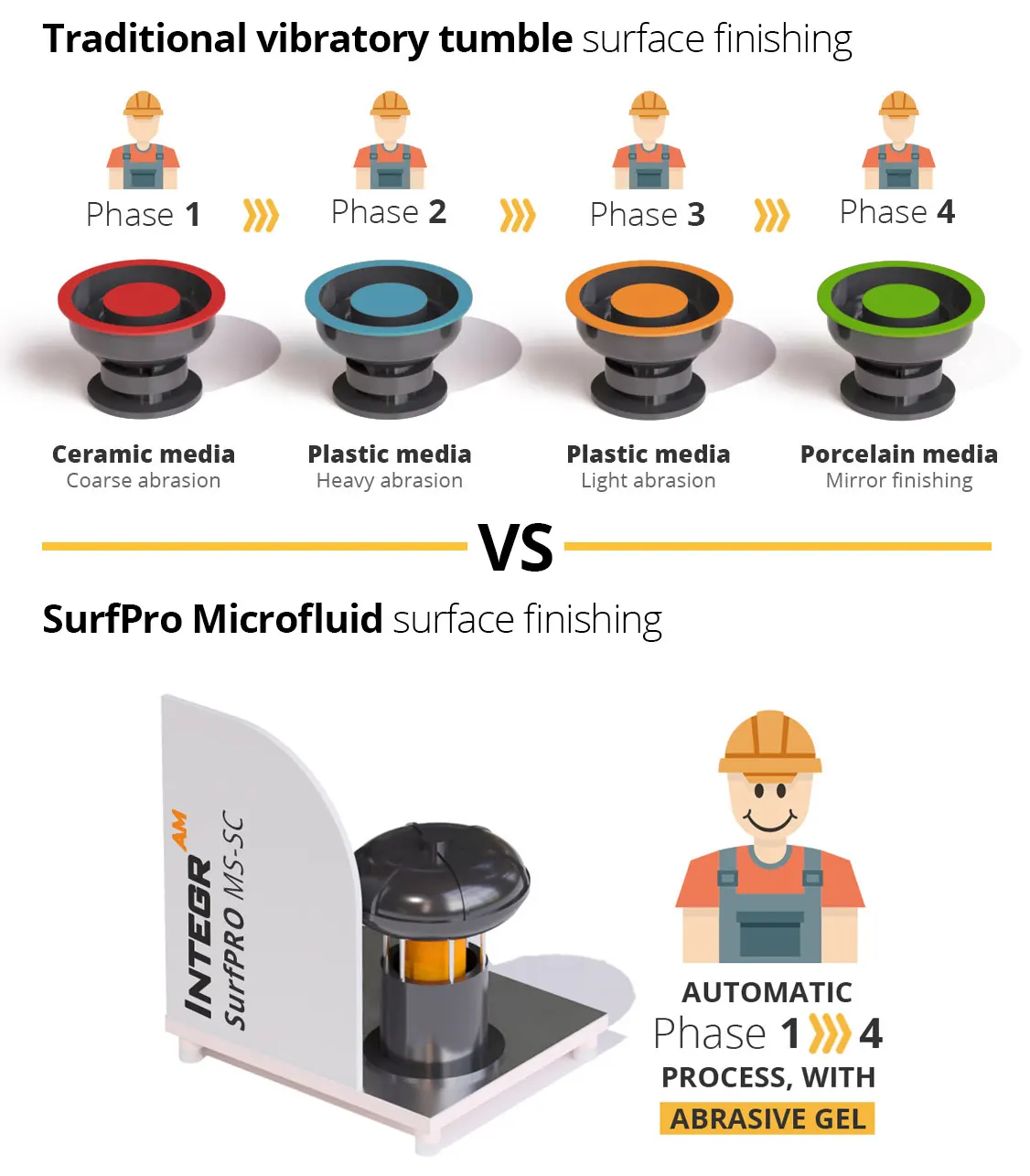
The SurfPro Microfluid advantages
What sets the SurfPro Systems apart from the other finishing systems, is the Microfluid technology, which brings multiple advantages.
- Affordable
With just one machine you can perform all the steps aforementioned, without the need for human intervention: just put your parts in the machine, load your recipe, and press play. Less hardware in your factory, less labor, and a low TCO (total cost of ownership) granted by low-cost consumables and extremely low maintenance needs.
- Gentle with small features
Compared to other mechanical finishing technologies, the patented SurfPro process is much more gentle, allowing to reach extremely low Ras without destroying thin details and preserving sharp corners.
- Automatic
SurfPro brings a new level of “affordable automation” to the surface finishing world.
Once started, the machine will dose automatically the different gels, and perform automatic cleaning after each cycle. Apart from pressing “play”, the operator only needs to load the parts and unload them at the end of the process. - Flexible
The SurfPros are fully programmable by the user: time per each cycle, the quantity of gel to be used, duration of the wash cycle, etc. If needed, you could even convert it into a traditional tumbling machine!
Before and after
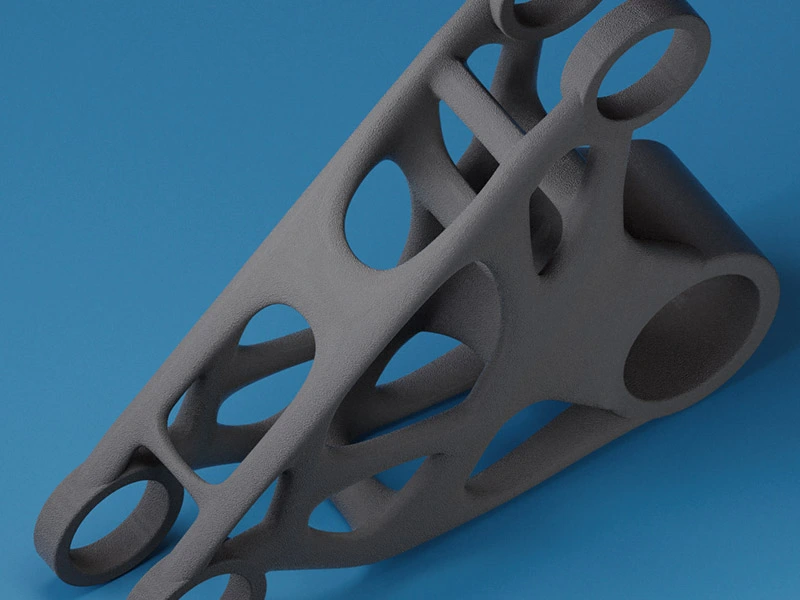
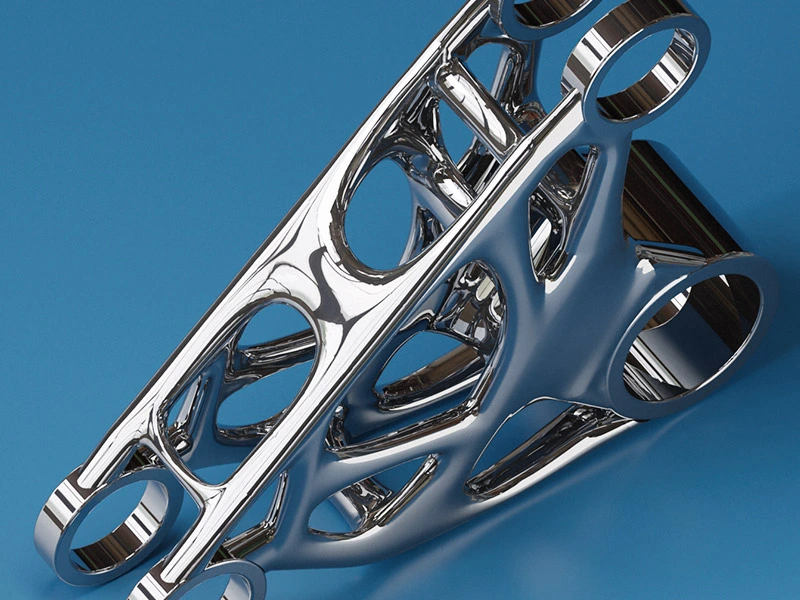
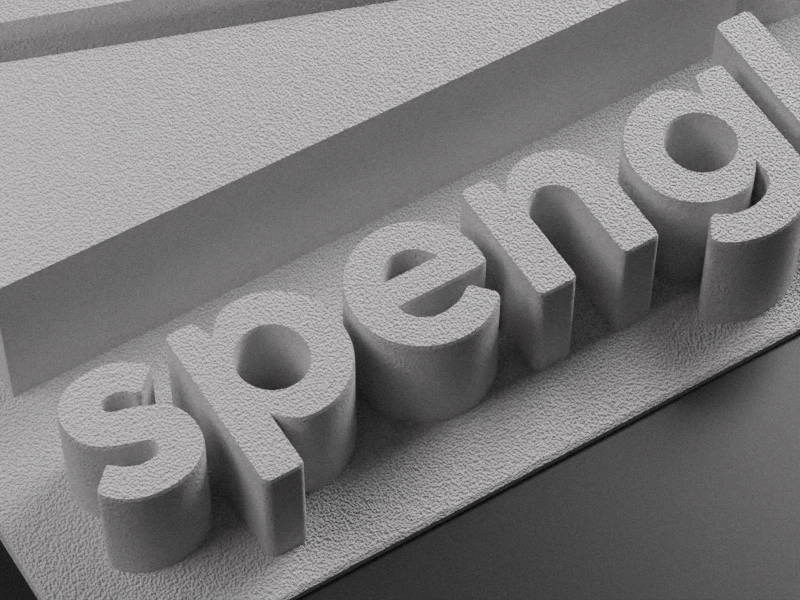
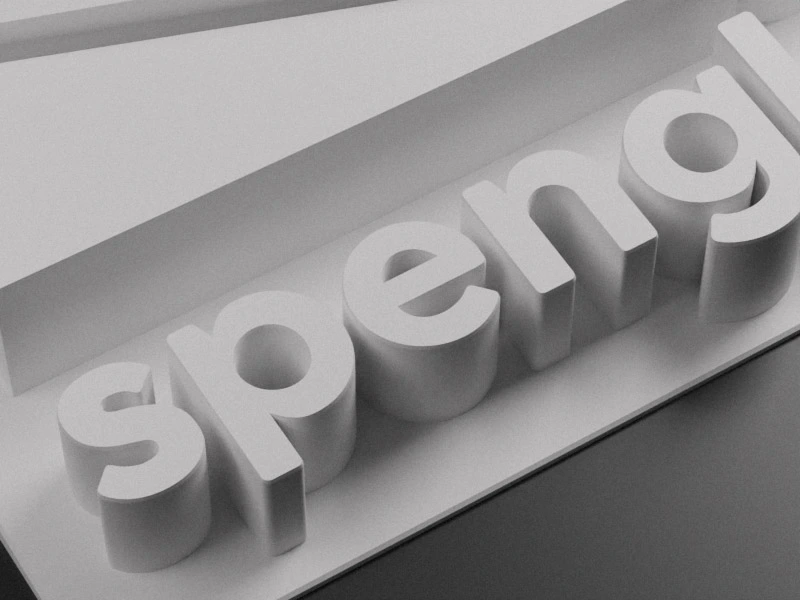
Fields of application
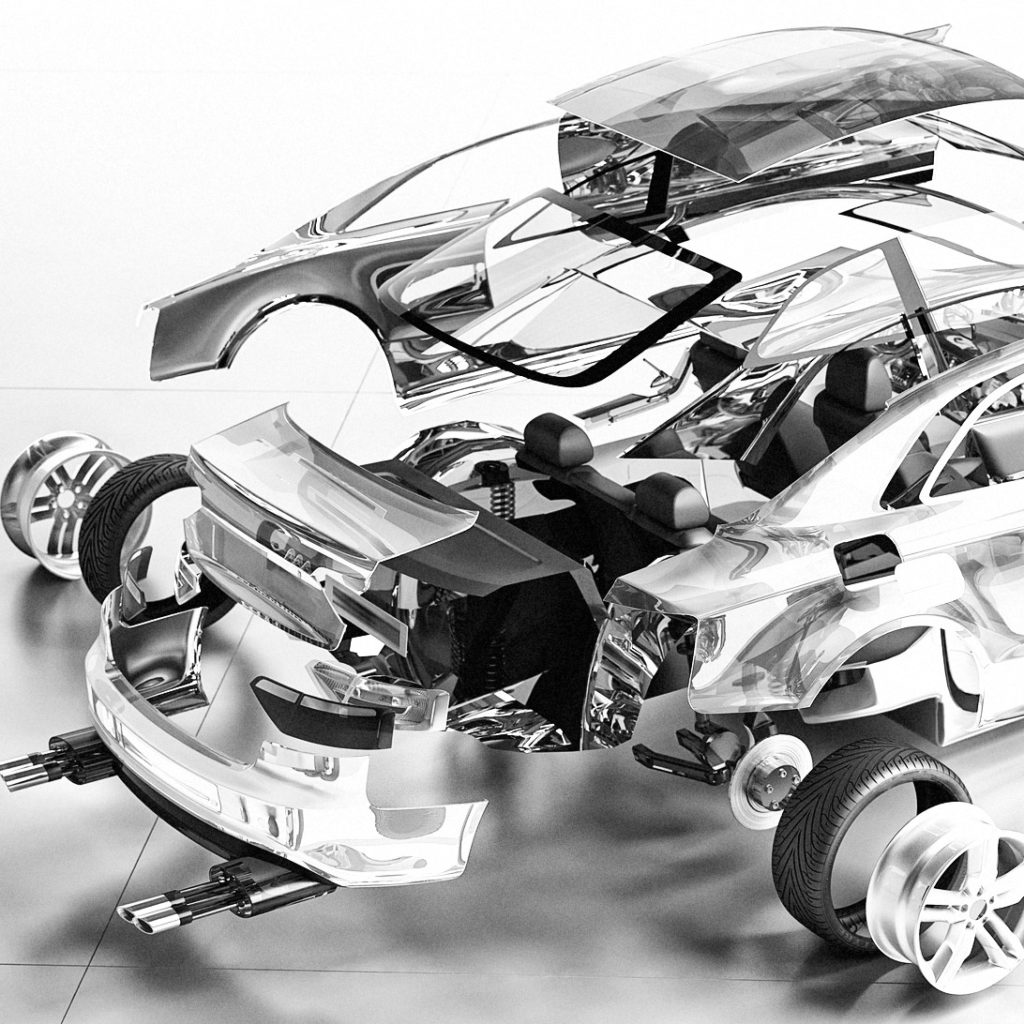
Automotive applications
3D printing is increasingly being used to create automotive parts due to its flexibility, speed, and cost-effectiveness. However, 3D-printed parts often require post-processing to achieve the desired surface finish, and this applies both to plastic and metal components.
Sometimes additively manufactured parts have functional applications, and they need low Ras to reduce mechanical friction with other elements, or to prevent grease and oil from stagnating over the coarse surface of an SLM or Electron Beam printed part.
Other times the aim may be purely aesthetic, and the goal is to achieve maximum brilliance by minimizing the visibility of the layers, while preserving texturing, engraving, and relief at the same time.
When we talk about automotive and 3d printing, it can be about one-offs for special customers, as well as mass customization. But in both cases, the SurfPro systems deliver the optimal mix of automation, process personalization, and care for fine details.
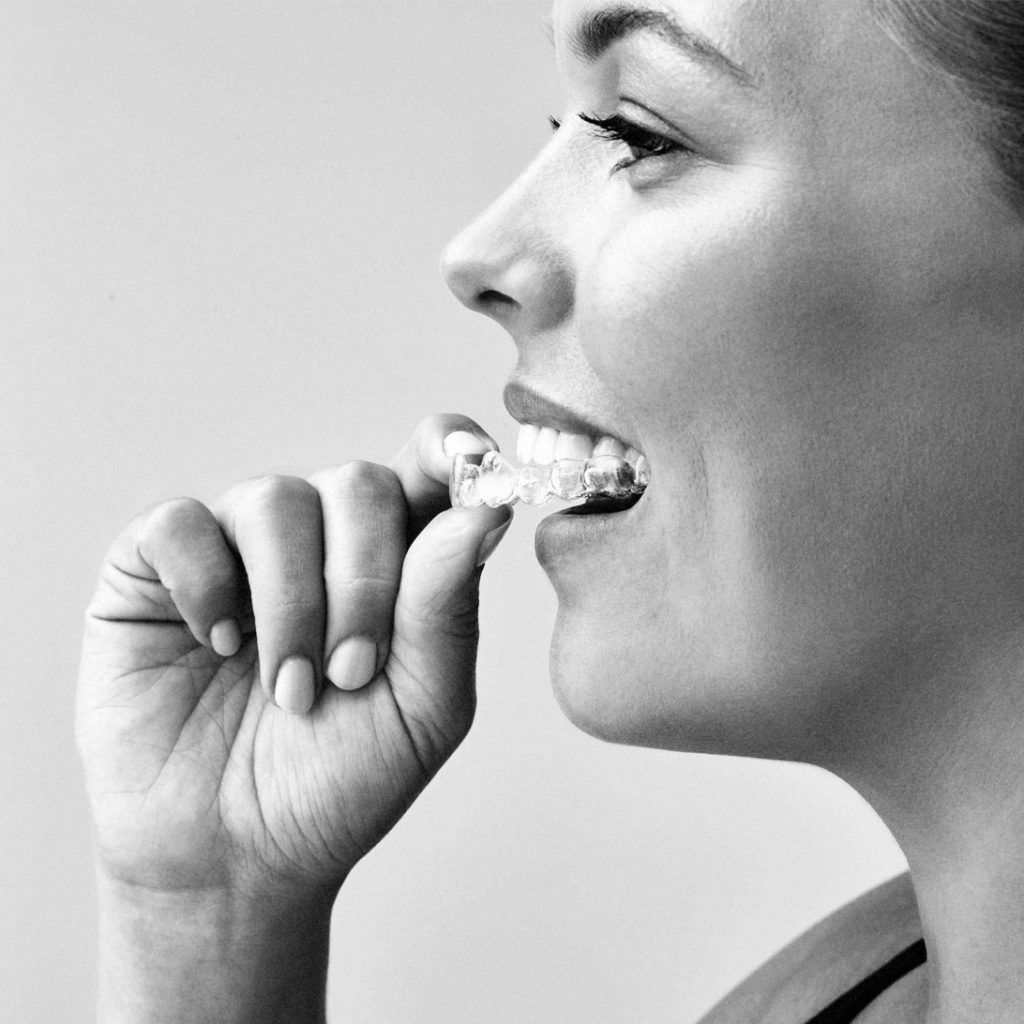
Dental applications: clear aligners, removable partial dentures, and bridges
Surface finishing is an important step in the production of clear aligners and partial dentures, as it helps to ensure patient comfort, aesthetics, and proper fit.
With our SurfPro BS we deliver cost-effective mass polishing and filing for clear aligners’ contours.
And to perfectly polish metal RPDs and bridges, we have ultra-fast tools that will remove any roughness from the surfaces. For more info on this: info@spengler.tech.
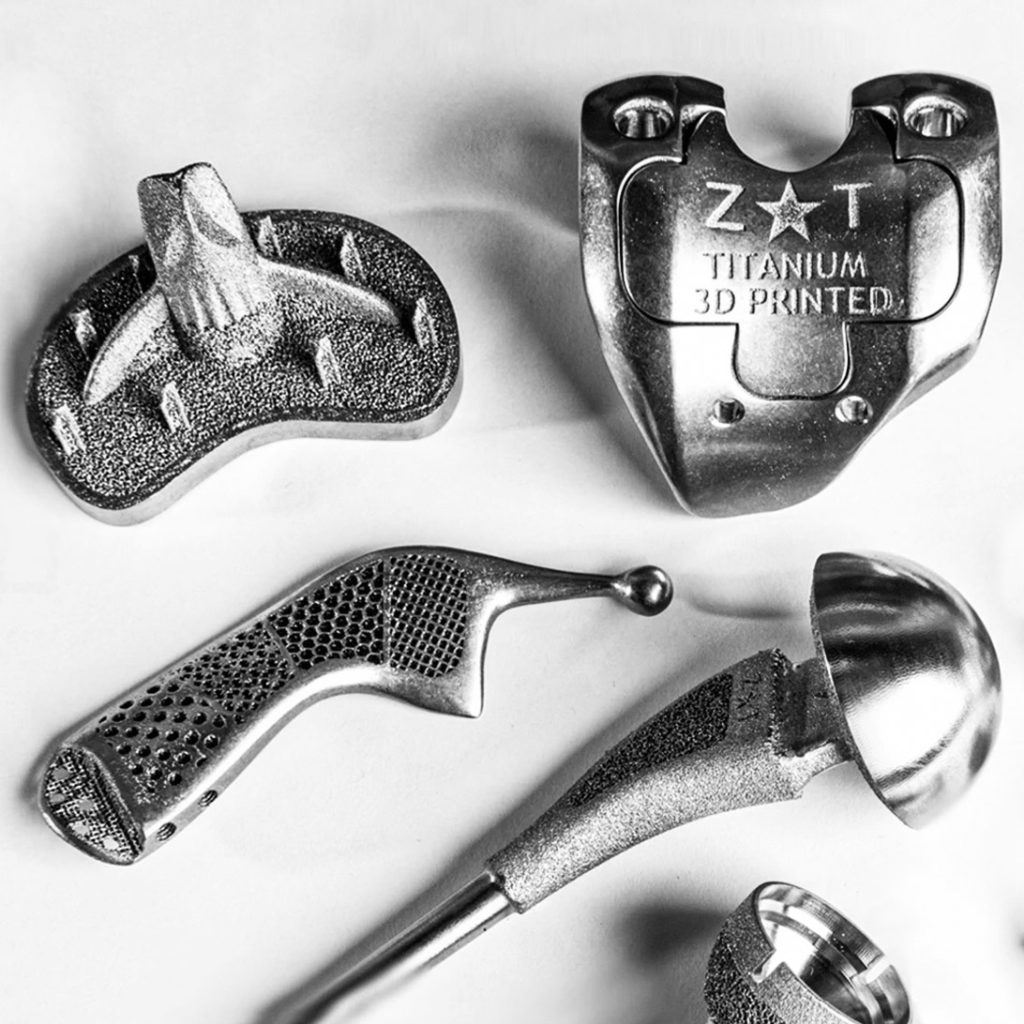
Medical applications: from nylon to titanium to peek
Surface finishing is a crucial step in the production of 3D-printed prostheses and implants, that can be manufactured – depending on the final application – in many different materials, including standard nylons like PA12 and PA11, metals like titanium and steel alloys, as well as high-performance polymers like PEEK (polyether ether ketone).
In combination with machining, used to drill size-perfect holes and to create high precision milled surfaces, the rugosity reduction delivered by systems like the SurfPro Microfluid is fundamental to bring customers implants and prostheses featuring state-of-the-art biocompatibility, functionality, and aesthetics.
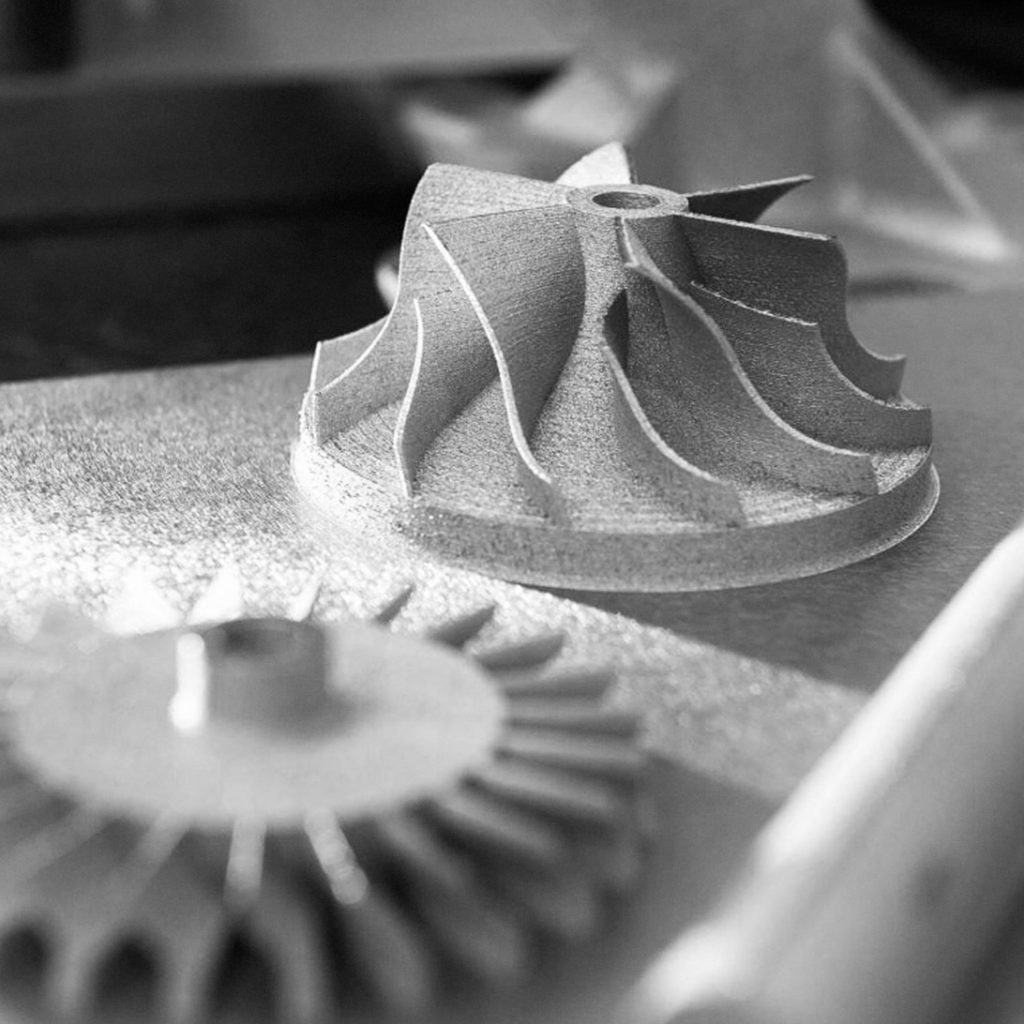
Aerospace: turbine blades and antennas
3D printing has numerous applications in the aerospace industry, from prototyping and testing to the production of end-use parts, and two cases that truly require great surface finishes are turbine blades and antennas / waveguides.
The design freedom brought by additive manufacturing brings on the table new challenges in terms of surface finishing, since both for the optimization of the flux and for a correct reflection of the radio waves, regular surfaces with minimal roughness are essential.
In this context, thanks to the abrasive force and delicacy in the treatment of small details that distinguish Microfluid technology compared to more traditional methods, the results that can be obtained with SurfPro systems are exceptional.
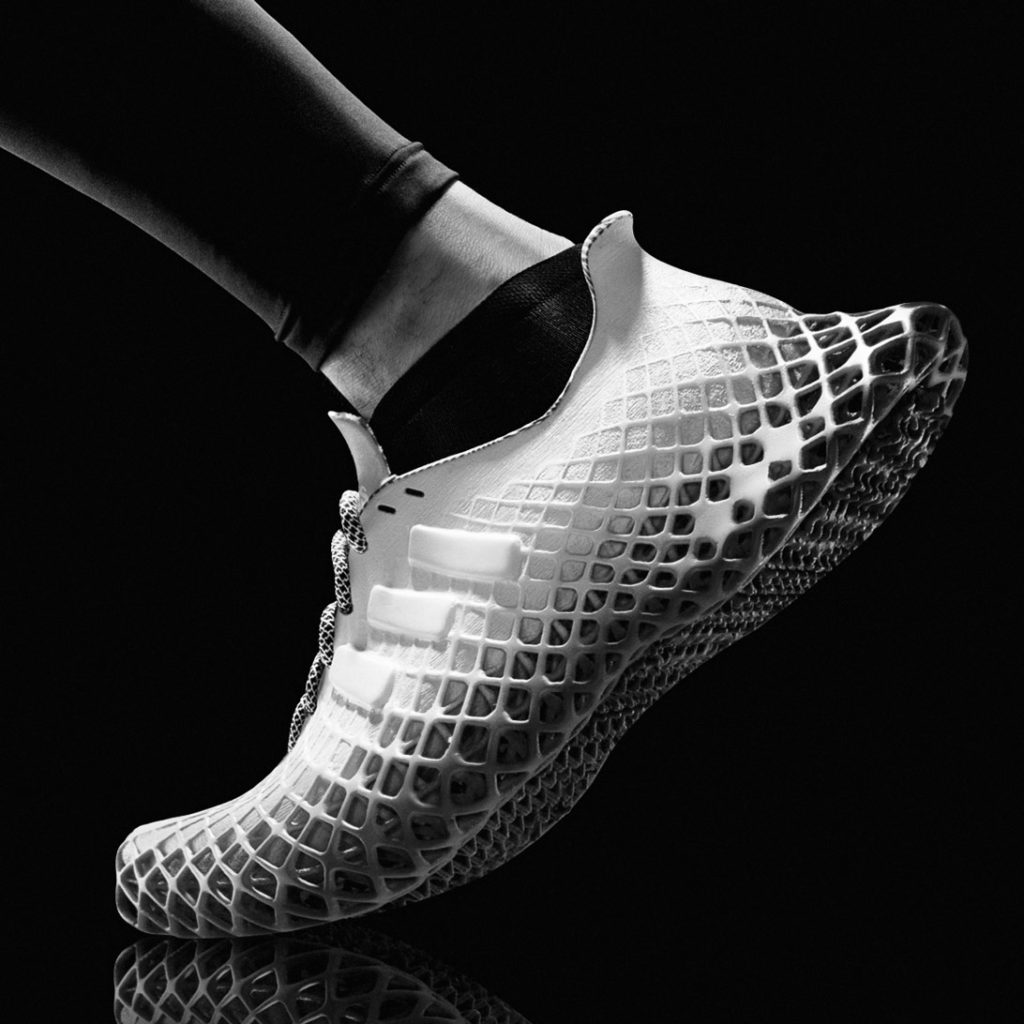
Consumer goods: mass customization
Besides the classic “product prototyping”, one of the most promising applications of 3D printing in consumer goods is mass customization. Traditional manufacturing techniques are designed for mass-production of identical goods, which can limit consumer choice and personalization. Additive manufacturing, on the other hand, allows for the creation of individualized products on a large scale, providing consumers with unique and tailored goods.
On the other hand, mass additive production always need mass post-production, in order to get a surface quality as much as possible on par with injection molding.
And the level of automation delivered by the SurfPro Microfluid systems is the perfect answer, allowing consistent, repeatable and predictable results batch after batch.
The Models
SurfPRO BS
For plastic and metal
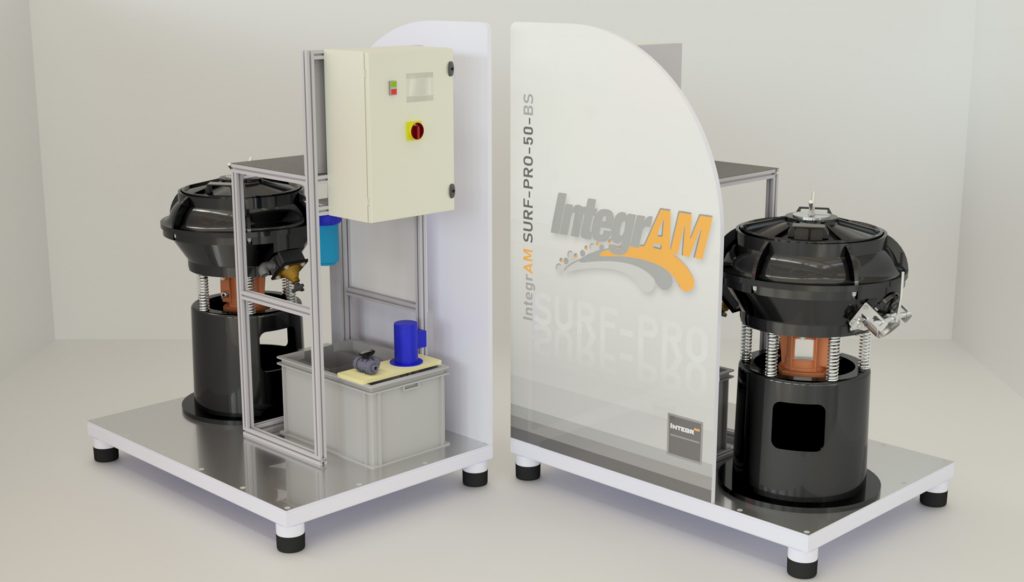
SurfPRO MF
For plastic and metal
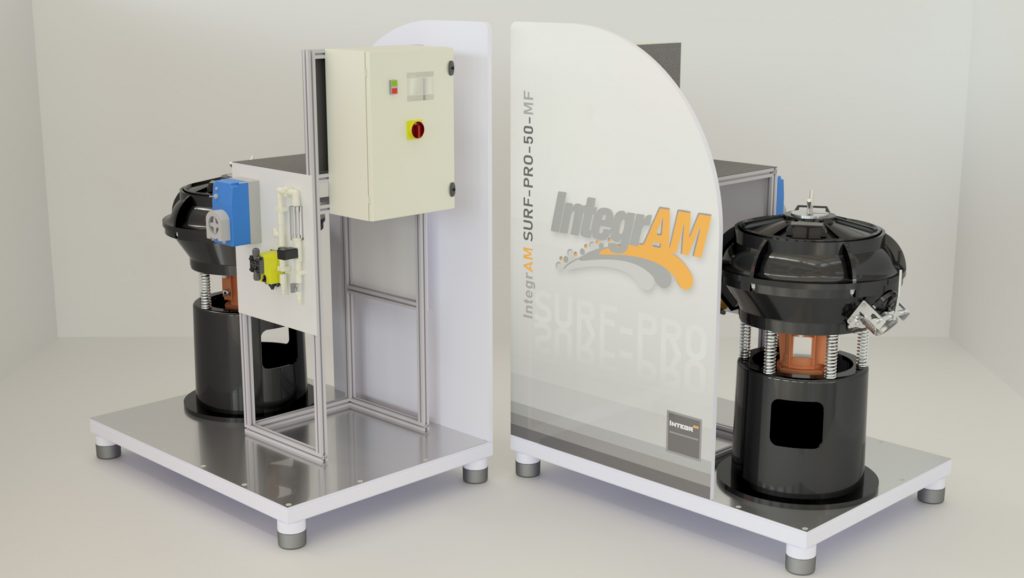
SurfPRO ABK
For metal
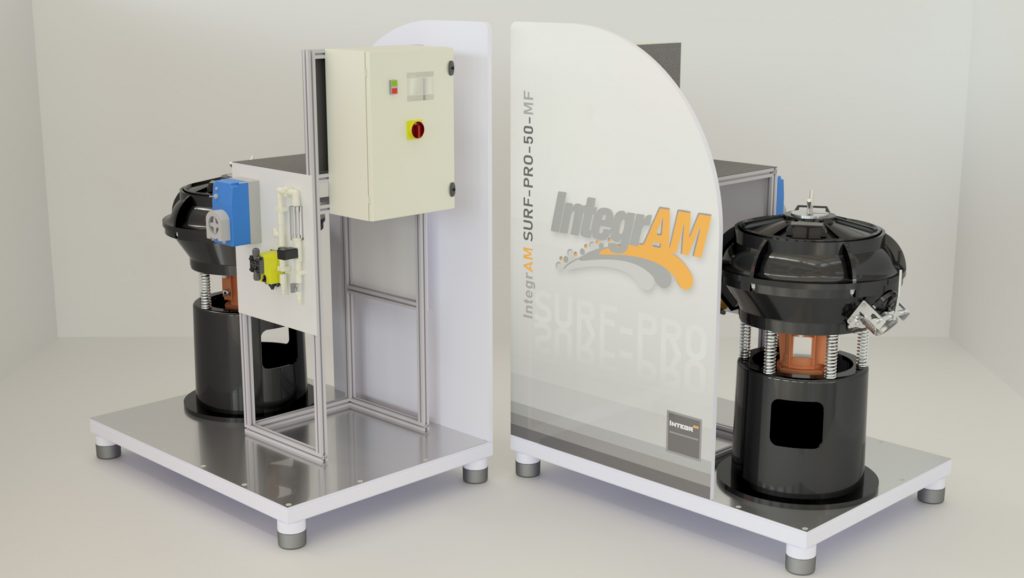