The limits of traditional bead-blasters
for SLS and MJF powder removal
Every owner of a PBF 3D printer knows the hassle of manually blasting every single part removed from the powder cake.
For small, desktop or lab 3D printers like the Lisa or the Fuse 1 this doesn’t really represent a problem: printing volumes are small, and most of their users can accept to spend some hours per week manually bead blasting their parts.
But when it comes to EOS, 3D Systems, Farsoon, or HP systems, things change: those machines are fast, with build volumes ranging from 50 to more than 200 liters. You need automation, if you want to have a sustainable and rentable workflow.
And while on the market there are automatic bead blasting tools, based on the old concepts of rotating barrels and belts, we feel there are limitations that make those systems may be good but not optimal.
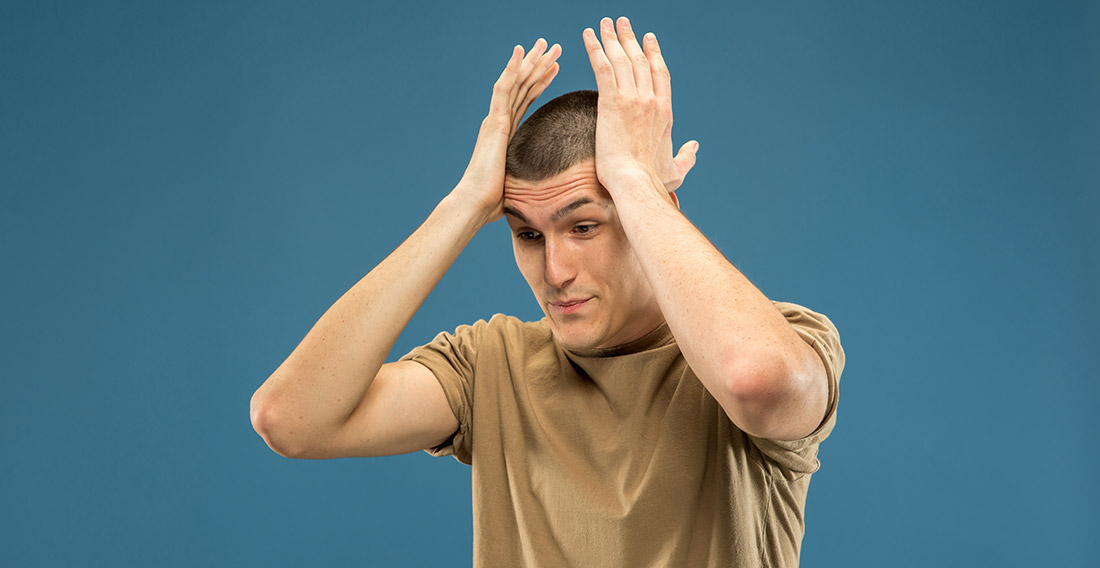
The main limitations of traditional blasting systems
First limitation:
The kinetics
This can cause parts to break, and it certainly makes it difficult to impossible to process massive and thin parts in the same batch.
Second limitation:
The volumes
On the market, there are barrel and belt bead blasters with available volumes ranging from 30ish to 60ish liters, with the latter of course positioned in the upper part of the price range.
And while a 30-liter system can appeal to many, it’s quite limited for anyone who needs to process big parts or many parts because he owns more than one 3D printer. And this without thinking at the limitation nr 1.
Third limitation:
Cost-per-volume
IntegrAM VibroBlast technology
A new take on automatic depowdering for PBF 3D Printing
And so, what does the VibroBlast technology bring to the post-processing automation table? We will take the chapter above as a base to illustrate the advantages.
Benefit #1: THE KINETICS
With the VibroBlast machines, the parts to be blasted lie on (and inside) a bed of elastic vectorial media that has the following functions:
- Allow a free 360 degrees rotation of the parts inside the vat
- Serve as a damper between the parts, limiting the possibility of a direct impact between them
- Help remove the powder that remains attached to surfaces even if it shouldn’t (because of overheating during the print, or powder aging). So, somehow replicate what you normally do with your fingers when you clean the parts manually.
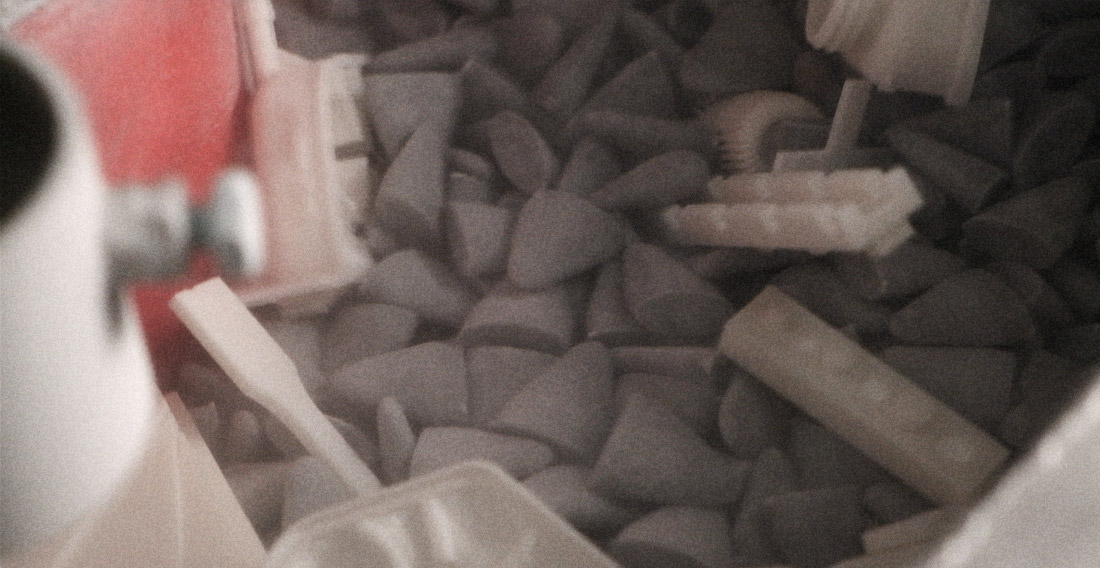
Your parts are in good “hands” (elastic vectorial media, that also work as shock-absorber)
Benefit #2: THE VOLUMES
VibroBlast’s toroidal processing vats have volumes ranging from 50 up to 520 liters, with an available volume of 2/3 of the nominal value.
This makes our systems ideal for any type of production, from mid-sized machines like the EOS Formigas up to 3D Systems sPro230s. And everything in between.
Benefit #3: ROI
Besides the aforementioned benefits, our systems also have the best cost/volume ratio, making it an excellent choice not only from a technical point of view but also from that of the ROI.
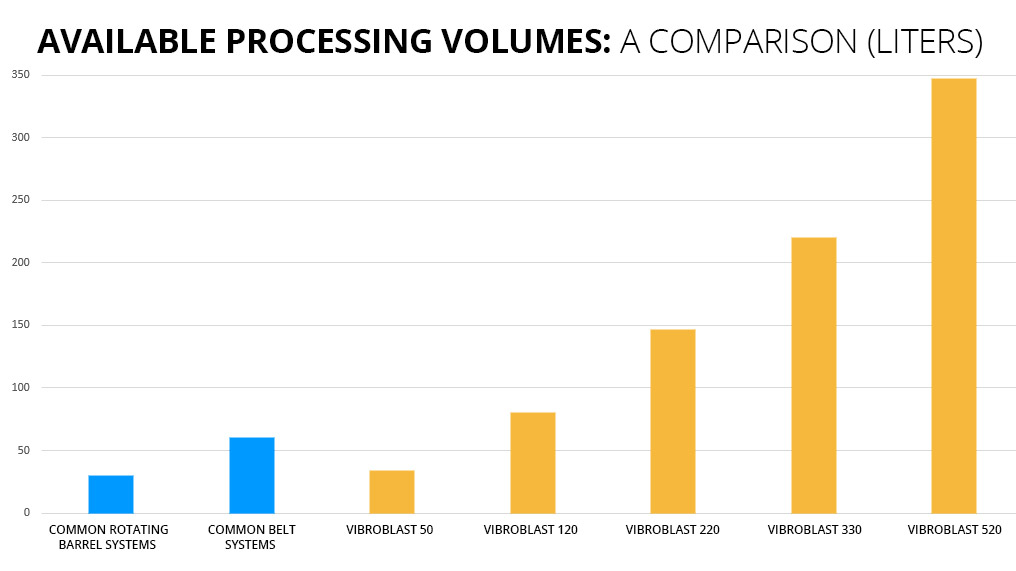
The volume range covered by the VibroBlast series expands the limits of what you can depowder, both in terms of size and quantity.
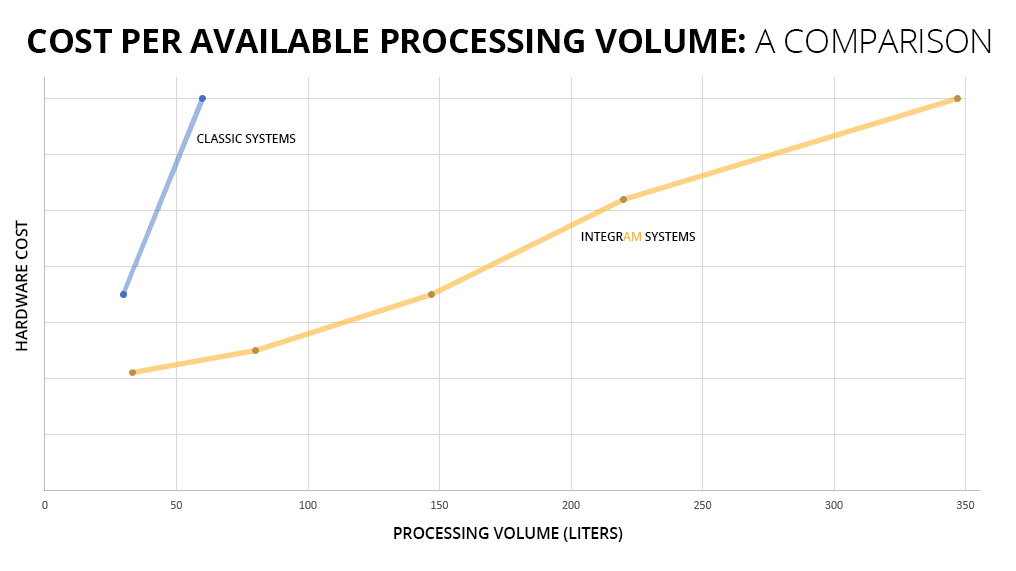
A chart that puts in comparison the average cost-per-volume of the VibroBlast systems versus the classic solutions we can find in the additive manufacturing market.