SVR Powder sieving systems
Industrial-grade sifters for SLS and MJF 3D printers
Good powder sieving plays a crucial role in optimizing the performance, efficiency, and quality of powder-based polymer 3D printing processes. It ensures uniformity, enhances flowability, reduces defects, and ultimately leads to higher-quality printed parts with consistent mechanical properties.
Our SVR sieving systems, designed and built in Europe with the highest standards in mind, feature industrial-grade hardware, to allow high and consistent throughput rates, without compromise.
They are available in different sizes and configurations, to match the specific needs of our customers:
- Carbon steel and INOX versions
- Diameters from 400 mm up to 1200 mm
- Single or double sieve, for 2 or 3 degrees of separation
- Nylon 12, 11 and TPU configurations
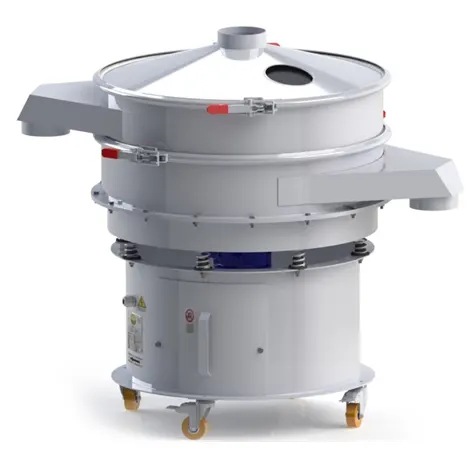
Sieving solution for your specific productivity needs
For light workloads
Eg: Sinterit Lisa,
Formlabs Fuse 1,
Eos Formiga, etc.
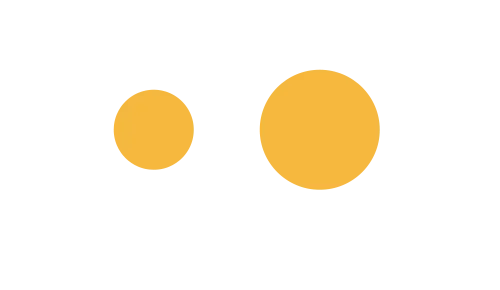
For medium workloads
Eg: EOS Formiga,
Farsoon eForm or 252P,
Prodways ProMaker P1000 S/X, etc.
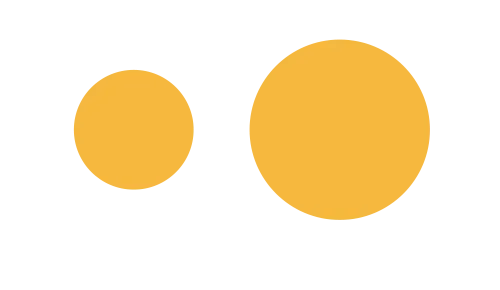
For heavy workloads
Eg: Eos P396 / P500,
3D Systems sPro 60, SLS 380, SLS 300,
HP MJF5200, etc.
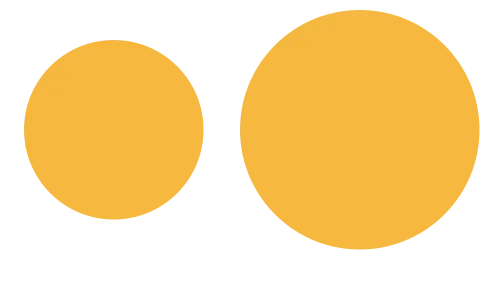
All trademarks, logos and brand names are the property of their respective owners
THE 8 KEY ADVANTAGES OF PROPER POWDER SIEVING
Good powder sieving is essential for powder-based polymer 3D printers for several reasons: