How to bring true automation to
Surface finishing for 3D printing & CNC machining
Traditional vibratory finishing – also called tumbling or tribofinishing – is a widely known process for mass-finishing metal and plasticparts.
In this batch-type operation, pellets of abrasive media and the parts to be processed are placed into the tub of a vibratory tumbler. The tub of the vibratory tumbler and all of its contents are then vibrated. The vibratory action causes the media to rub against the workpieces, which brings to the desired result: a smoother surface finish.
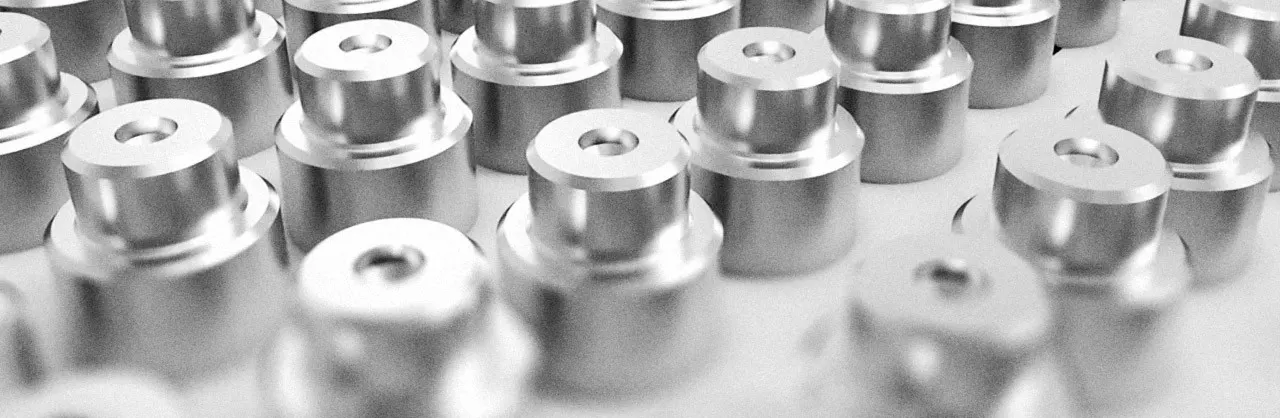
When does vibratory post-processing become necessary?
CNC-manufactured parts always usually have a relatively good surface finish right out of the machine, but good does not mean perfect: for some specific applications, the need to reach extra-low Ra (rugosity) values is crucial. Hence, post-processing of those parts is mandatory.
Coming to 3D printing, while the advantages of this way of producing are obvious, the well-known average poor surface quality of the printed parts surely represents one of its weaknesses. Some technologies perform better than others, but no one gets even close to CNC machining. So if the target is to reach mirror-like or even just uniform matte surfaces, post-processing becomes an essential step in the production workflow.
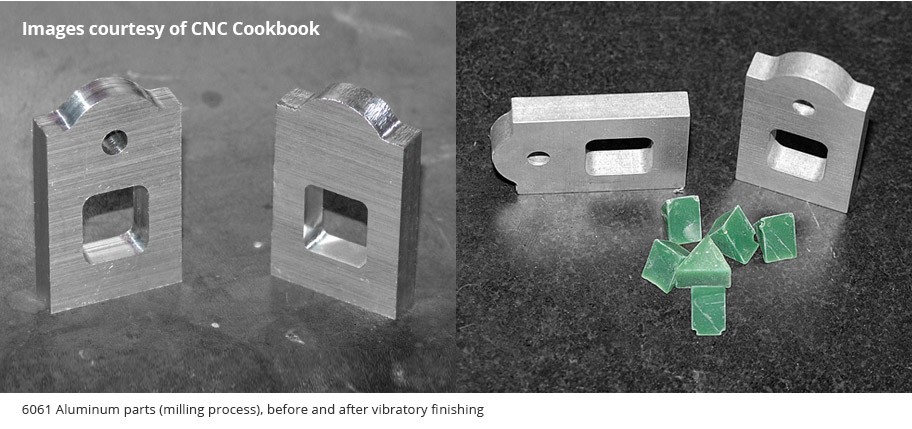

And concerning metal post-processing, vibratory finishing is one of the first techniques that come to mind, sometimes associated with a shot peening pre-process.
Note: We will not cover here heat treatments like annealing and HIP processes, or chemical ones, but we might write something interesting about surface hardening and density improvement processes in the future.
Anyway, in a world where automation becomes more and more important, the traditional vibratory method shows its limits: it’s definitively a mass-finishing system, but it’s far from being an automated one.
Regardless of whether it is 3D printed parts or CNC machined pieces, the process is the same: workpieces have to be processed through different abrasion stages, from the most aggressive to the gentler.
Usually, the process requires up to 4 vibratory systems, each loaded with different tumbling media, and the parts have to be manually moved from one machine to another every time a cycle ends.
Or, you could have just one machine, and replace media between each step (after a careful cleaning), but that’s an even less optimized workflow, economically inefficient.
A new take on mass surface finishing with the SurfPro MicroFluid systems
Based on the patented Microfluid process, the IntegrAM SurfPro systems make use of media as conveying vector for the 3D printed objects, while the surface finishing is performed by in-house developed abrasive gels, capable to reach the most hidden features of the processed parts.
One single SurfPro MicroFluid does automatically what 4 separate vibratory systems do, and without the need of human intervention between each phase.
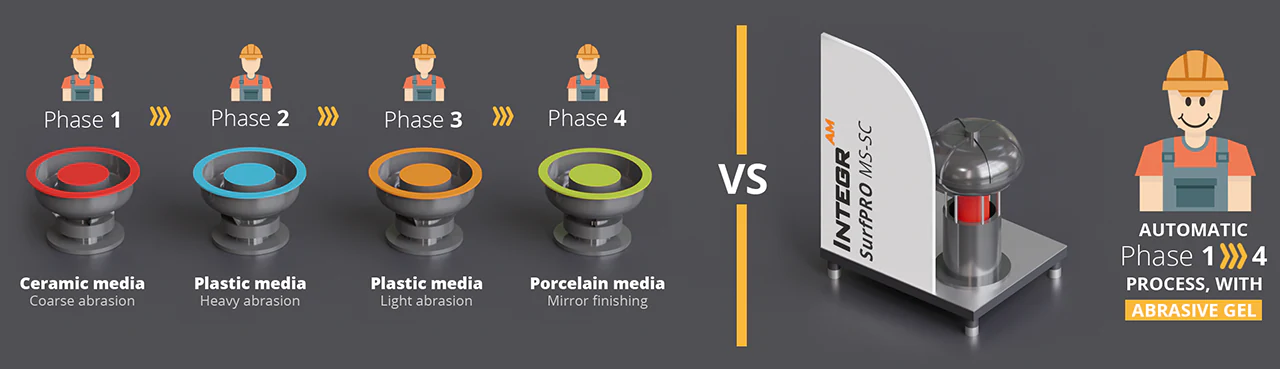
We can resume the advantages of the Microfluid technology in 4 points:
It’s
Affordable
It’s
Gentle
It’s
Fully automatic
SurfPro brings a new level of “affordable automation” to the surface finishing world.
Once started, the machine will dose automatically the different gels, and perform automatic cleaning after each cycle. Apart from pressing “play”, the operator only needs to load the parts and unload them at the end of the process.
It’s
Flexible