VibroBLAST Air system
Automatic powder removal for SLS and MJF 3D printers
VibroBLAST Air is the perfect 2-in-1 automatic depowdering and pre-finish tool for powder-bed additive manufacturing systems, the result of 8 years of research in close collaboration with sandblasting and air aspiration/filtration specialists.
Thanks to a patent-pending process that combines sand/shot blasting and vibratory finishing, VibroBLAST Air automatically depowders plastic parts manufactured with Selective Laser Sintering 3D printers / Multi Jet Fusion (HP).
Note: Another great VibroBLAST application is the automatic batch-blasting of metal parts 3D printed with DMLS® and SLM® systems. Click here to know more.
3D printed polyamides and more (SLS & MJF )
Our automatic powder removal VibroBLAST systems have been tested with PA12, PA11, charged or natural grade. But also with polypropylene and even CF-charged formulations.
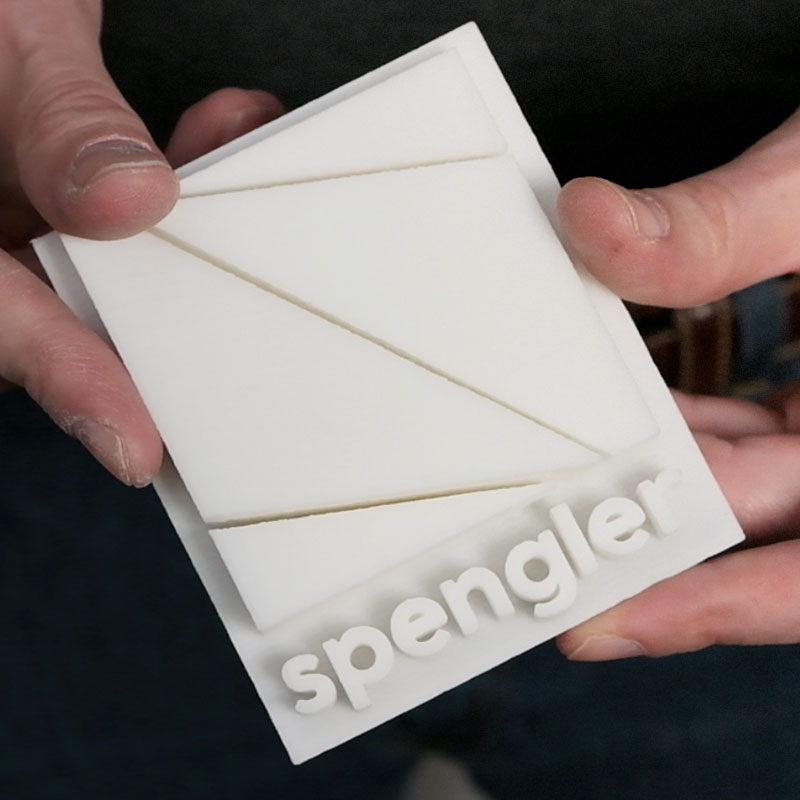
Thanks to the gentle kinetics, fine details are preserved from shocks with big parts. And the blasting action (single or double nozzle) reaches even narrow grooves and deep recesses.
3D printed TPU (SLS & MJF )
This custom-designed sole (courtesy of XFeet), characterised by a particularly intricate geometry, has been thoroughly cleaned fully automatically, showing no trace of residual powder.
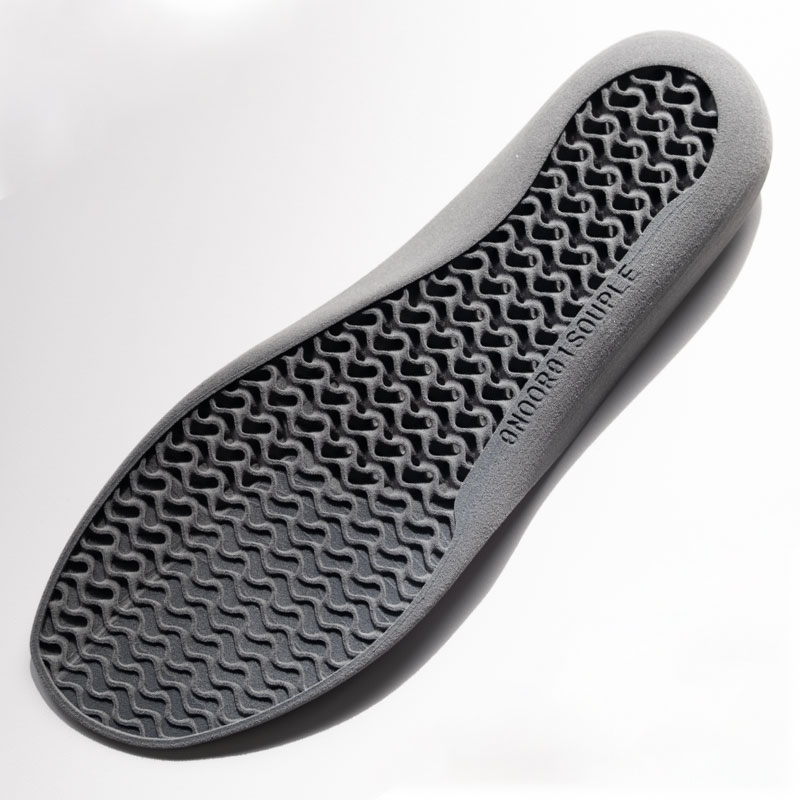
Depowdering TPU is a tricky operation, and high-productivity SLS printers can produce a large number of soles each day. The Super VibroBLAST is the perfect tool for this kind of application.
See it in action
Your parts are in good hands
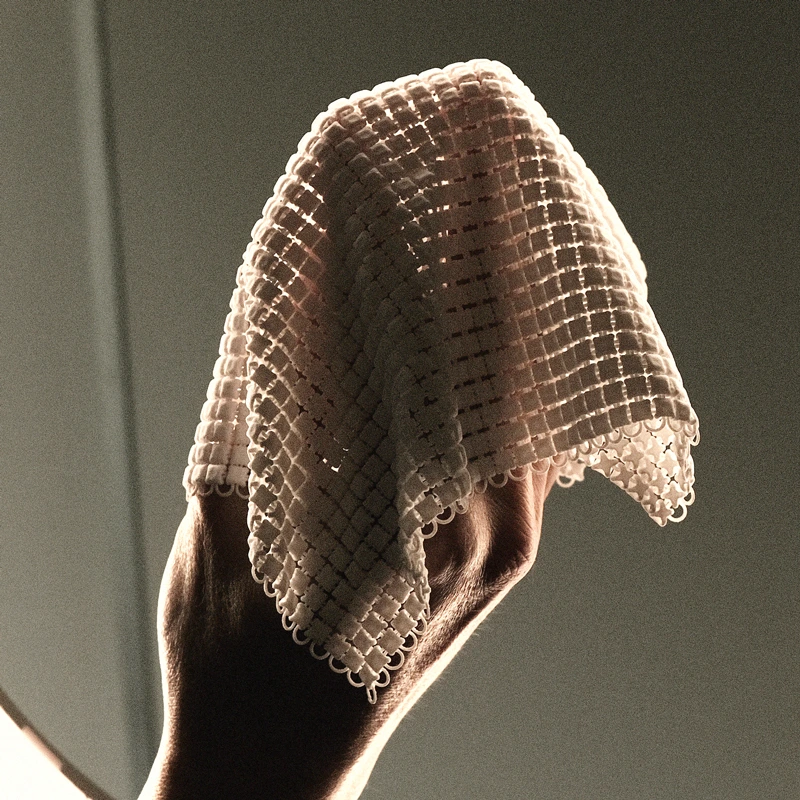
Different from everything else
What sets apart the VibroBLAST Air system from the many rotative sandblasting tools out there on the market?
While both feature automatic depowdering of the parts, the VibroBLAST Air uses “elastic” vibratory finishing media both as shock-absorber and as a three-dimensional movement vector for the 3d printed parts, exposing them to the blasting nozzles multiple times with always different angles.
Hence, compared to rotational blasters, the VibroBLAST Air is by its own nature much more delicate in the way it handles the 3D printed parts.
And of course, the elastic media also perform a soft abrasion action on the parts, something out of the scope of the traditional blasters, automatic or manual.
Contamination prevention
The PCCP versions of the system (Contamination Prevention, patent-pending) allow the cleaning of the parts by using the very same material of the printed objects (e.g. Nylon 12) as blasting media, so as to avoid even the minimal risk to “pollute” the parts.
Before & after
To better illustrate the results that you can expect from a VibroBLAST Air system, we made this practical before/after comparison on parts manufactured in Nylon 12 on a SLS® 3D printer.
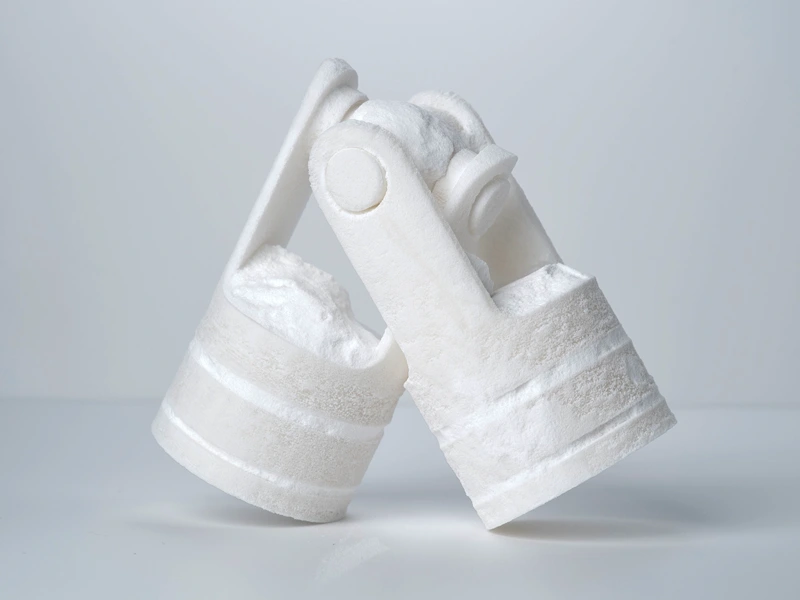
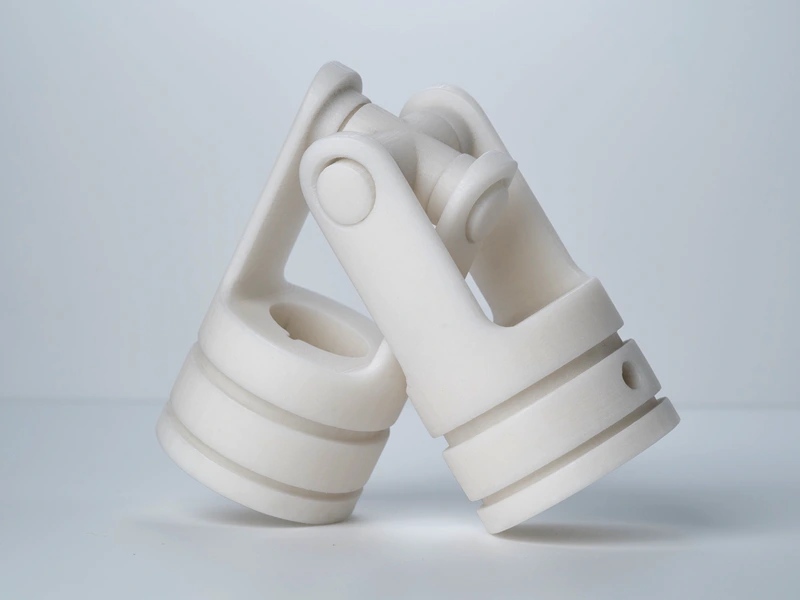
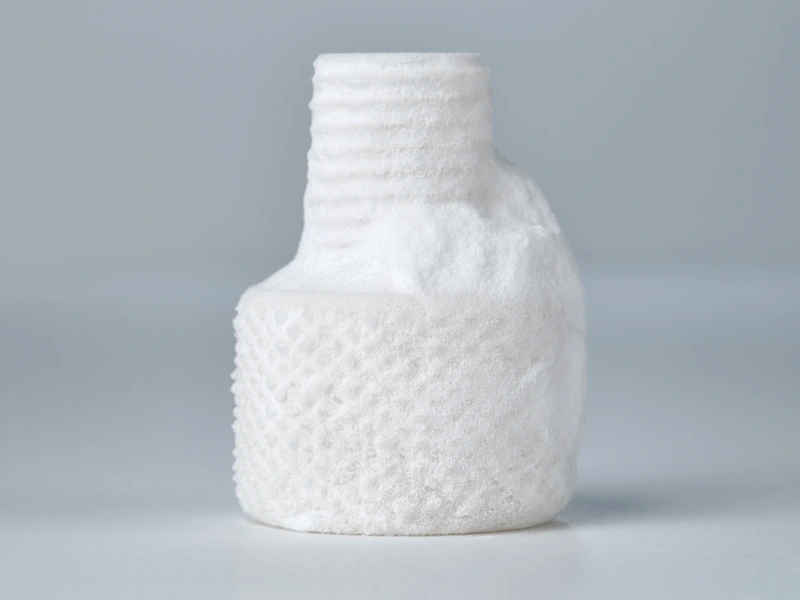
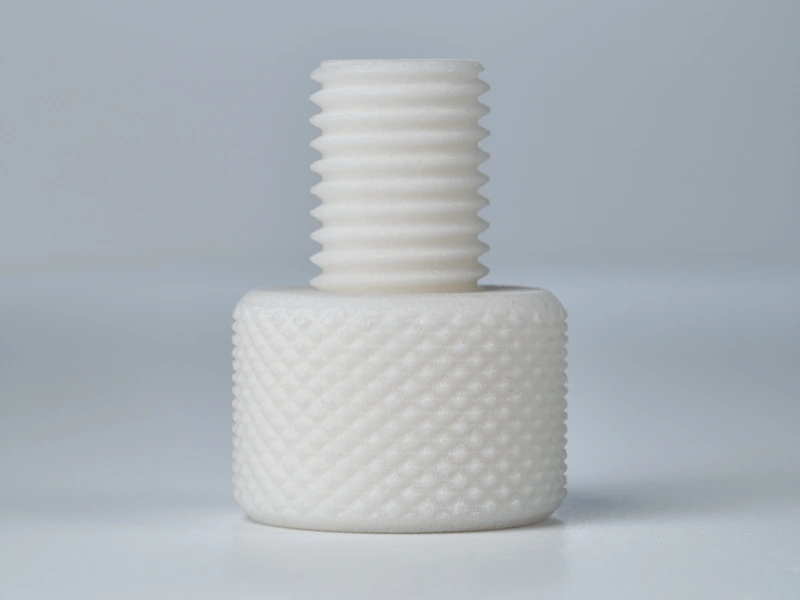
The VibroBLAST Air system is also at the heart of the all-in-one DCK solutions (Decaking, depowdering, pre-finish, powder sieving and recovery + mixing). Specifically developed for SLS® and MJF® systems, the DCK series is perfect for mid to high prodoctivity A.M. environments. [link]
VibroBLAST features
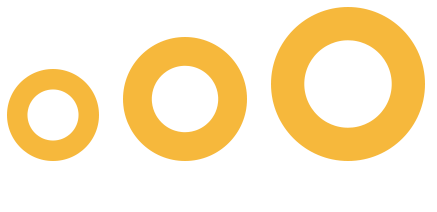
- VBA-DP: 3 sizes available
- VBA-PCCP-DP: Contamination prevention version, 3 sizes available
- Plug and play
- Siemens PLC control: Easy to use, with editable parameters
- Anti-static system
- Single blasting nozzle
- Self-cleaning filters (option)
Super VibroBLAST features
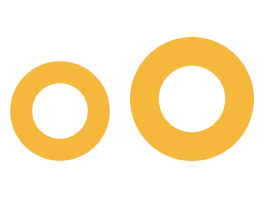
- For high-productivity environments
- SVBA-DP3: 2 sizes available
- SVBA-PCCP-DP3: Contamination prevention version, 2 sizes available
- Plug and play
- Siemens PLC control: Easy to use, with editable parameters
- Anti-static system
- Double blasting nozzle
- Triple media vacuum drain
- Self-cleaning filters (option)
Featured content and customers
Renault
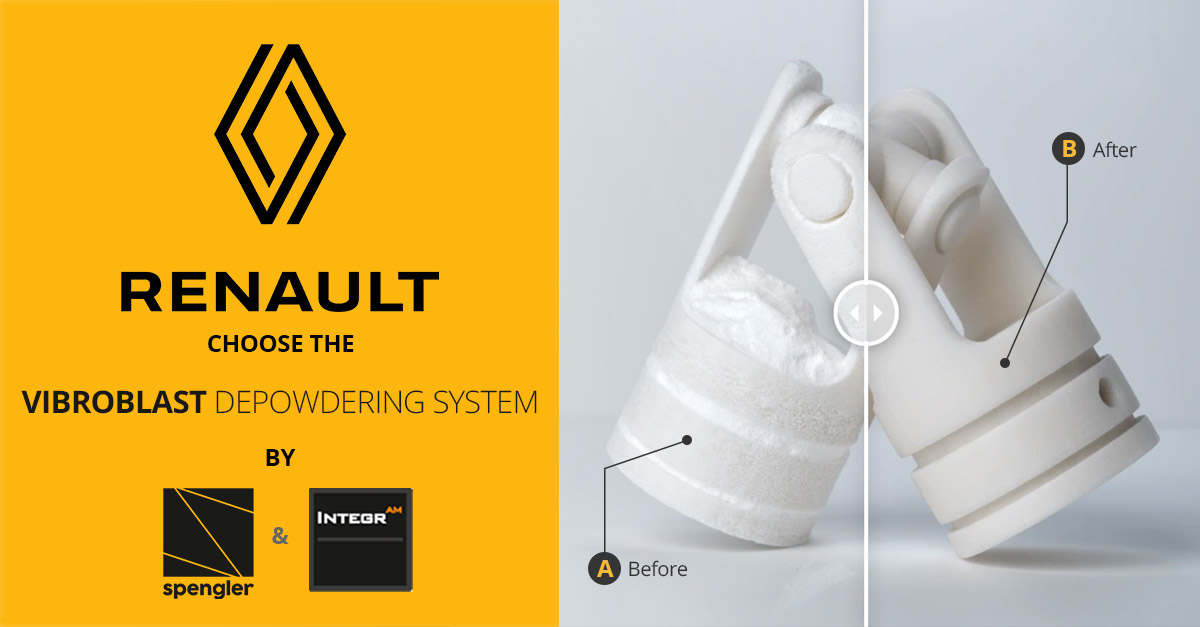
🚗 If anyone knows anything about automation, well, the automotive sector is the first one to look at. And Renault has been the French benchmark for the automotive sector since 1898.
🏆 So it’s easy to understand why we are happy that one of our automatic IntegrAM blasting systems is now part of their additive manufacturing pipeline, freeing up human resources from the tedious yet crucial job of removing the powder from SLS and MJF 3Dprinted parts!
Ref:
HP Additive Manufacturing (AM) Solutions – 3D Printing
3D Systems Corporation
ARRK
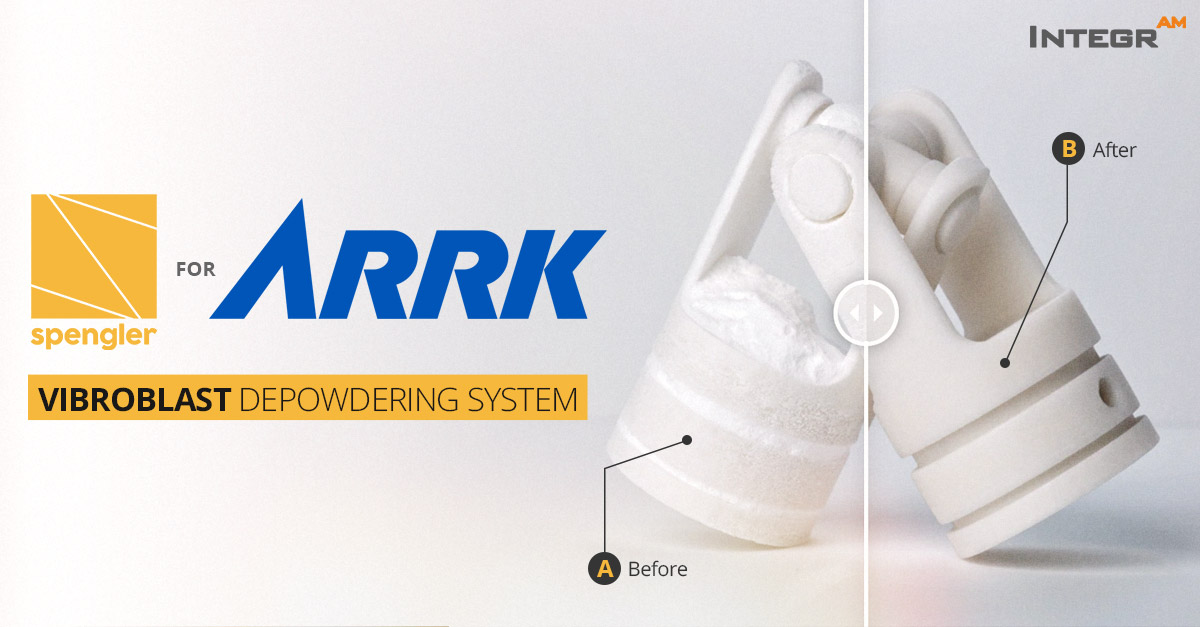
🚀 Proud and happy to announce that ARRK LCO chose the IntegrAM VibroBlast powder removal system for their SLS 3D printing department.
🙋🏻♂️ But why a VibroBlast system instead of a standard rotating-barrel or belt bead blaster?
📃 A look at this short article might give you some answers: https://lnkd.in/etFh3kam